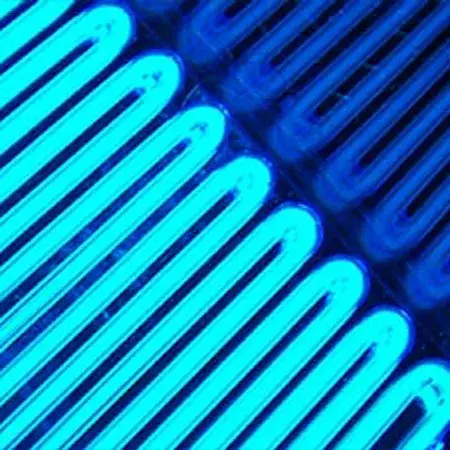
Samco’s UV ozone cleaning systems offer a sophisticated method for surface treatment by combining ultraviolet (UV) irradiation, ozone, and stage heating. This powerful, yet gentle process effectively removes organic contaminants from a wide range of substrates, including silicon, glass, and compound semiconductors such as GaN, SiC, GaAs, and InP. Available in compact benchtop and cassette-loading configurations, Samco’s UV ozone cleaners cater to both R&D and mass production environments, ensuring versatility and efficiency. With systems designed to handle a variety of materials, UV ozone cleaning is an ideal solution for those seeking a dry, non-invasive method for substrate preparation and contamination removal.
UV Ozone treatment
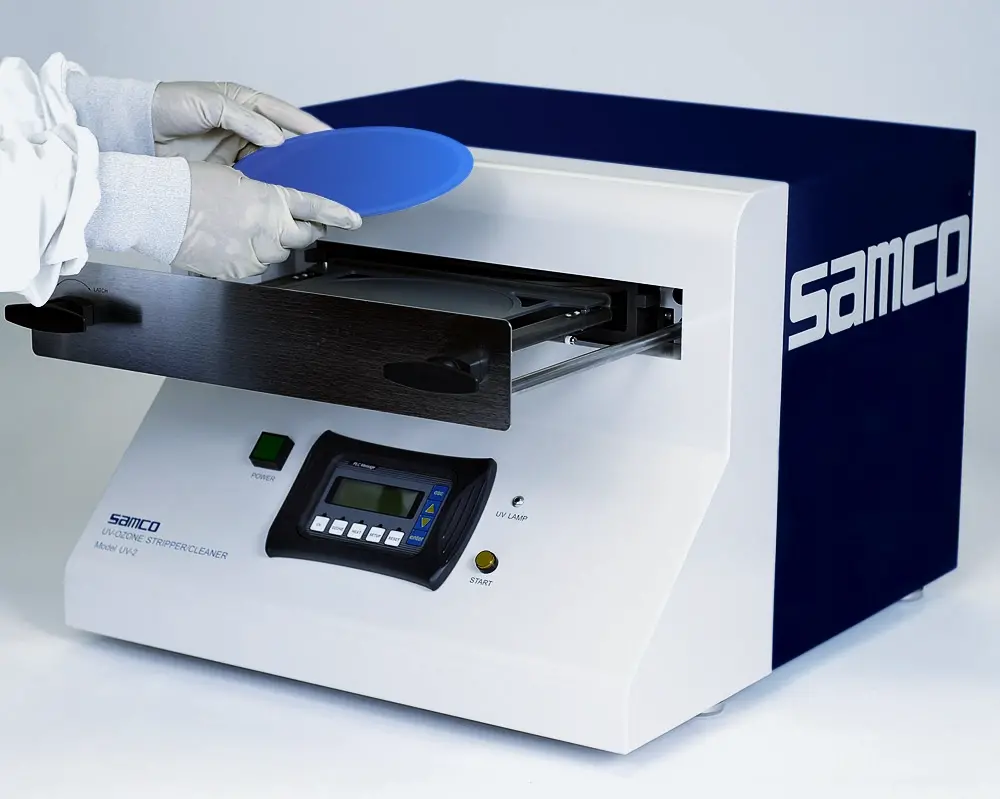
UV ozone treatment works by utilizing both 185 nm and 254 nm UV light wavelengths. The 185 nm UV light dissociates molecular oxygen into atomic oxygen, which reacts with ozone to form highly reactive singlet atomic oxygen. This powerful oxidant interacts with the substrate surface to remove organic residues, while the 254 nm UV light dissociates ozone, further enhancing the oxidation process. Additionally, stage heating plays a crucial role by accelerating ozone dissociation at higher temperatures, increasing the concentration of singlet atomic oxygen and improving cleaning efficiency. This process results in the removal of organic contaminants without causing damage to the substrate, making it particularly useful for sensitive materials like semiconductor wafers. The UV ozone cleaning systems also feature an ozone decomposition unit and automatic nitrogen purging for enhanced safety, ensuring a completely dry, chemical-free treatment.
COP samples treated with UV Ozone and stage heating, along with ozone flow, maintained stable hydrophilic surfaces for 180 days, demonstrating the long-term effectiveness of UV Ozone treatment compared to oxygen plasma.
Products
Ozone generator provides a higher ozone concentration and sample stage heater allows process temperature control up to 300°C. These features increase the reactive oxygen species during the process and improve the etch rate.
Products
UV Ozone Ashing of Photoresist
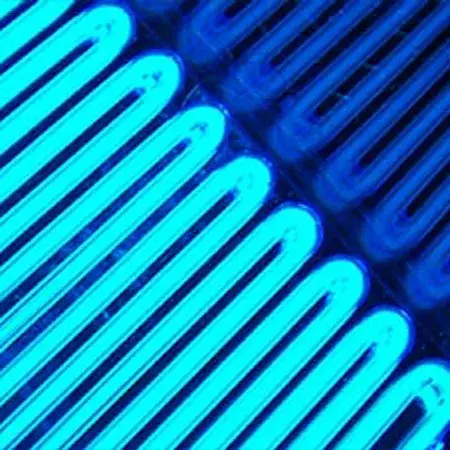
UV Ozone ashing is a versatile, dry, and solvent-free process that provides a gentle alternative to plasma ashing. Utilizing neutral oxygen radicals generated through UV light and ozone, this method eliminates the risk of physical and charging damage caused by ion bombardment in plasma-based methods. It is particularly advantageous for processing damage-sensitive materials like low-k dielectrics, ensuring effective photoresist removal while preserving substrate integrity. UV Ozone ashing is also environmentally friendly, producing no hazardous effluents, making it a sustainable choice for advanced device fabrication.
How UV Ozone Cleaning Works
UV Ozone ashing relies on two critical mechanisms: UV irradiation and temperature control. A dual-wavelength UV lamp emits 185 nm and 254 nm light. The 185 nm light generates ozone (O₃) by dissociating molecular oxygen, while the 254 nm light breaks ozone into highly reactive singlet atomic oxygen (O(¹D)). This singlet oxygen chemically reacts with substrates, oxidizing inorganic surfaces and breaking down organic contaminants into volatile byproducts like CO₂, H₂O, and O₂.
Stage temperature plays a crucial role in enhancing the density of reactive oxygen species. Higher temperatures accelerate ozone dissociation, increasing the concentration of singlet oxygen. For photoresist ashing, elevated temperatures significantly improve process rates, offering faster and more efficient cleaning for even the most challenging applications.
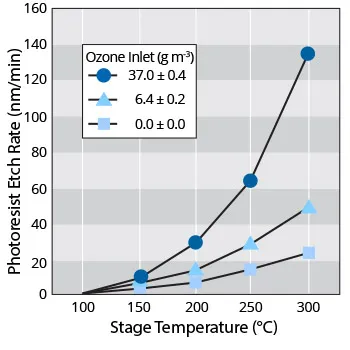
Applications of UV Ozone Ashing
UV Ozone ashing extends beyond photoresist removal, supporting a variety of material research and device fabrication needs:
- Surface cleaning of silicon wafers, III-V compound semiconductors (e.g., GaAs, InP), and plastic packages.
- Adhesion improvement for direct bonding (e.g., glass, PMMA, COC).
- Surface activation and wettability enhancement for microfluidic channels.
- Organic contamination removal and surface modification of polymer substrates.
Samco’s UV Ozone systems offer a comprehensive, damage-free solution for these applications, ensuring reliable performance across diverse materials and processes.
Advantages of UV Ozone Ashing
Damage-free processing for sensitive materials
Unlike plasma-based methods, UV Ozone ashing avoids ion bombardment, which can degrade electrical properties and damage sensitive device layers. This makes it ideal for applications involving low-k dielectrics or substrates requiring minimal physical stress. Additionally, UV Ozone ashing is a completely dry process, eliminating the need for wet cleaning chemicals and hazardous effluent disposal. Samco’s systems include an integrated ozone killer to safely decompose exhaust ozone, ensuring a cleanroom-friendly operation.
High-efficiency ashing
Samco’s UV Ozone cleaners leverage advanced features to enhance ashing efficiency. Ozone generators boost the concentration of reactive oxygen species, while stage heating optimizes the process temperature. With precise control from ambient to 300°C, higher densities of reactive atomic oxygen are generated, accelerating photoresist ashing rates. These capabilities make the process ideal for high-throughput environments and demanding applications.
System versatility
Samco’s UV Ozone ashing systems support a wide range of wafer sizes, from 100 mm to 300 mm, and offer configurations tailored for both R&D and production. Optional cassette-to-cassette wafer loading improves throughput in manufacturing environments, while table-top systems provide cost-effective solutions for smaller-scale operations. The systems are designed to handle diverse applications beyond photoresist ashing, including surface cleaning of III-V semiconductor wafers, organic contamination removal, adhesion improvement, and surface oxidation.
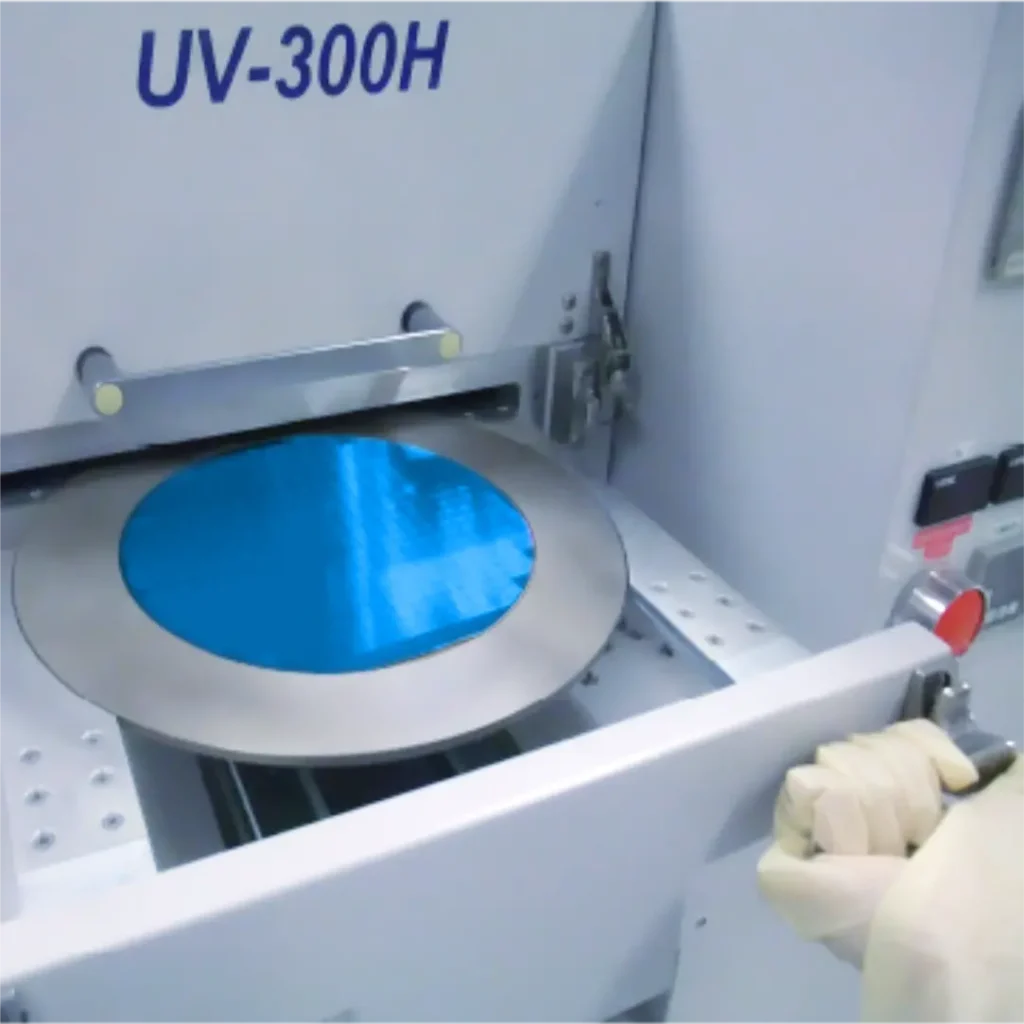
Samco’s UV Ozone cleaners achieve high-speed ashing by combining UV, ozone, and stage heating to generate reactive oxygen species and enhance etch rates. This process effectively removes organic materials like OMR-83, OFPR-800, and AZ-1350 without causing plasma damage.