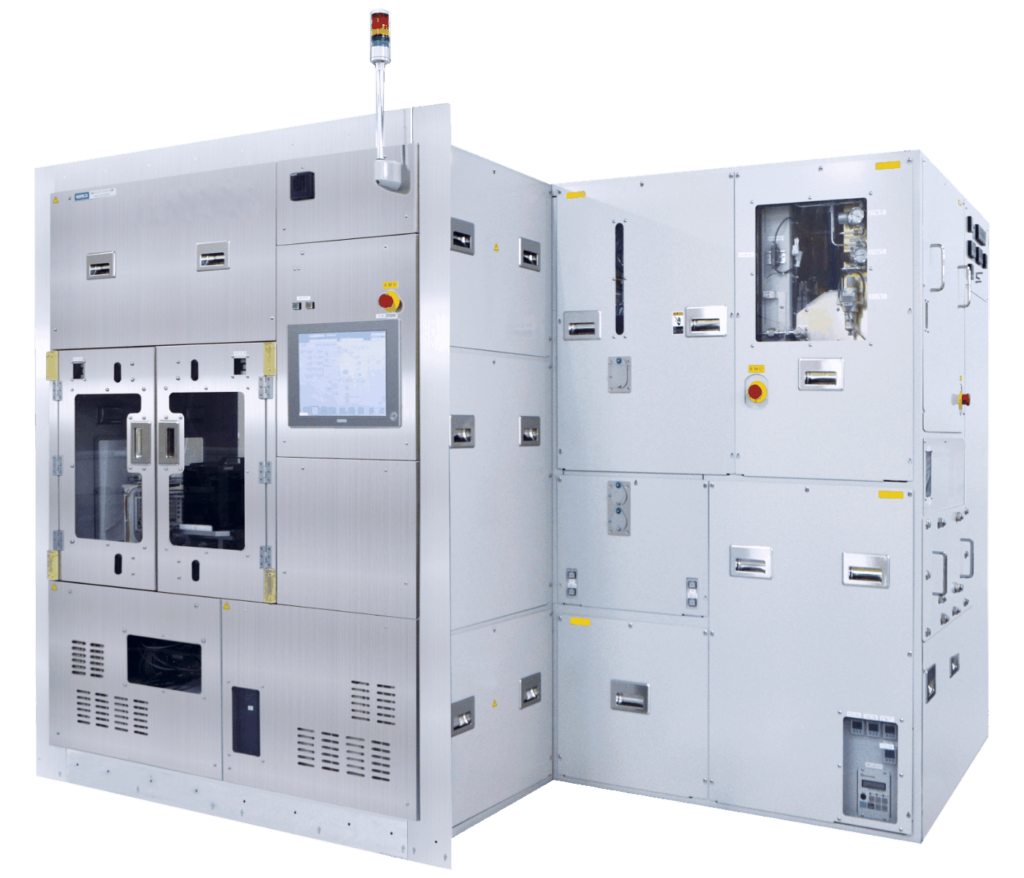
Samco was the first Japanese semiconductor process equipment manufacturer to provide Silicon Deep Reactive Ion Etching (DRIE) systems using the Bosch Process. We offer DRIE systems with a range of sample sizes and number of chambers for MEMS device fabrication and TSV via-hole etching. Our systems have industry-leading process capabilities, and the product lineup covers both R&D and production. For high-volume device manufacturing, a double reaction chamber specification is also available.
DRIE System Lineup
Key Features & Benefits
- Industry leading etch rates of over 50 μm/min
- High selectivity of over 250:1 (Si:Photoresist)
- Uniformity of ±5% or better (ø4, 6, and 8″ wafers)
- High aspect ratio (greater than 100:1)
- Low scalloping, smooth sidewall profile (less than 0.1 μm scallops)
- Patented, dual frequency silion on insulator (SOI) anti-notch etching technique
- Unique “anti-tilt” feature that ensures high uniformity
- Electrostatic chuck and helium backside cooling (for wafer temperature control)
- ICP source can be modified for etching of SiO2