Introduction
Since its founding, our company has been developing and designing equipment with superior environmental, health, and safety (EHS) features. In 2016, we launched the Aqua Plasma® cleaner, which utilizes water as its primary material, characterized by being safe and environmentally friendly. The product has been well received by many customers. The Aqua Plasma® process generates H, O, and OH radicals during discharge. These radicals enable the reduction of surface oxide layers on metals like gold, silver, and copper, decomposition of organic matter, superhydrophilization, and bonding. We currently provide batch-type systems capable of processing irregularly shaped substrates and diverse product types. However, as wiring becomes increasingly miniaturized and three-dimensional, the demand for wafer processing has risen. To meet this demand, we have developed a single-wafer Aqua Plasma® system featuring a wafer-handling robot.
Equipment Overview
The single-wafer Aqua Plasma® system utilizes the platform of our Etching, CVD, and Cluster systems. Compared to conventional batch systems, the single-wafer system features a sample stage optimized in both size and shape for wafer processing, achieving higher ashing rates and superior in-plane uniformity. Additionally, its compact reaction chamber allows for rapid evacuation and atmospheric release, ensuring advantages in both process performance and cycle time. Furthermore, options such as a vacuum cassette chamber and vacuum transfer system can be selected to prevent reoxidation after reduction. The system supports wafer sizes up to ⌀200 mm, with plans to accommodate larger sizes and square substrates upon request.
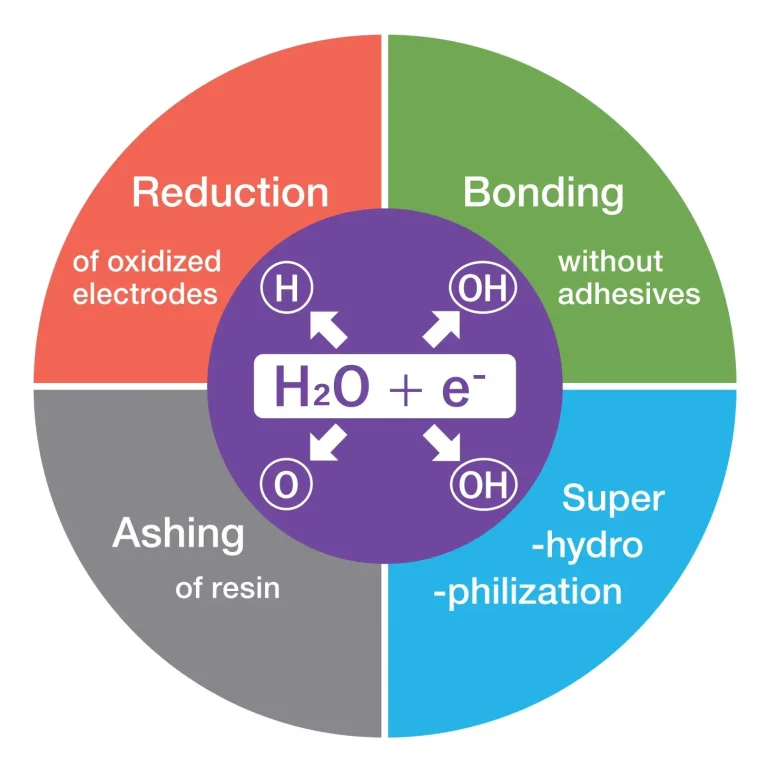
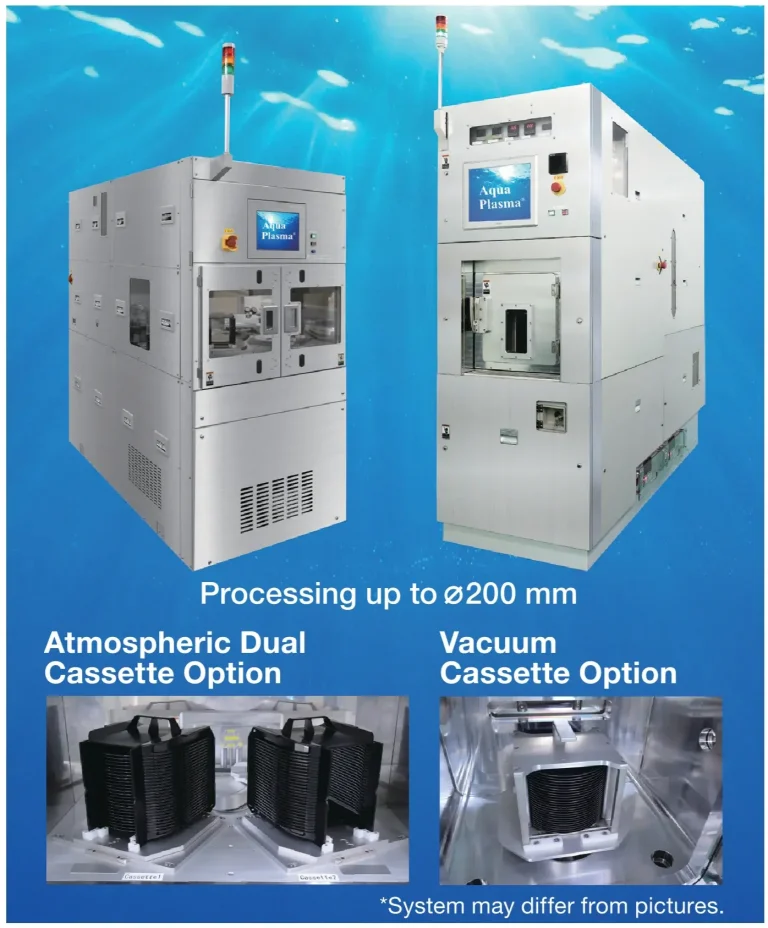
Performance
One of the most suitable applications for Aqua Plasma® is the descum process, which removes photoresist residues before plating or sputter deposition. During this process, exposed electrodes remain unoxidized, and the electrodes and resist sidewalls become hydrophilic. As a result, Aqua Plasma® improves electrical conductivity after plating, as well as the wettability and adhesion of the plating solution.
When ashing a ⌀200 mm silicon wafer with full photoresist coverage under standard descum conditions, the single-wafer Aqua Plasma® system demonstrated significantly higher ashing rates and in-plane uniformity compared to batch systems (Figure 3). Even when accounting for transfer times, the single-wafer system achieved three times higher throughput (Table 1) while ensuring minimal dimensional changes in the resist pattern and highly uniform processing. The system can process up to 24 wafers per hour at ⌀200 mm.
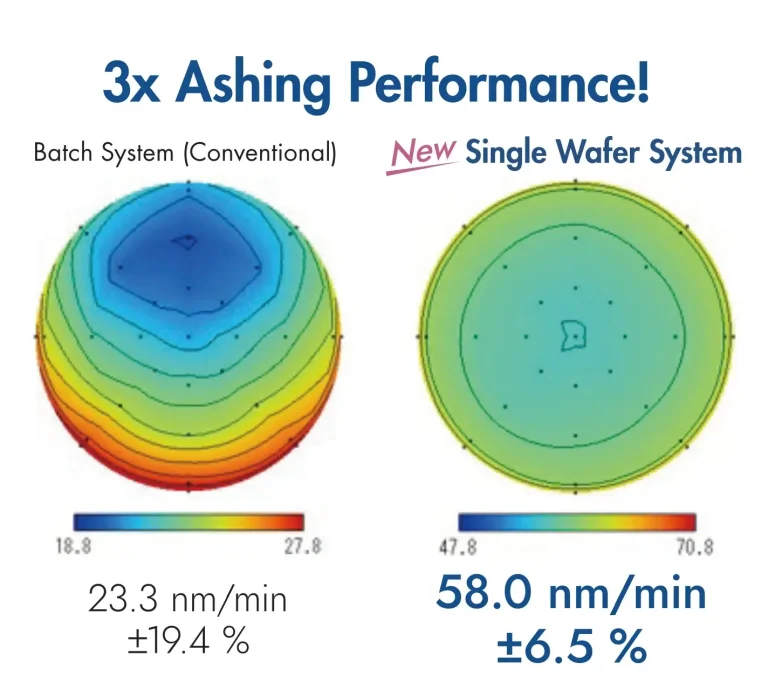
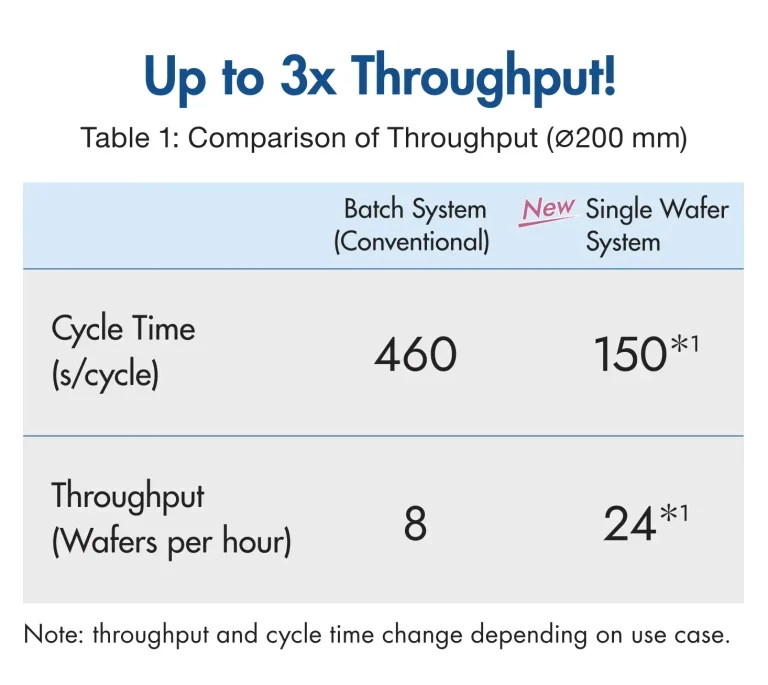
Conclusion
This technical report introduced the single-wafer Aqua Plasma® system. In addition to water vapor, the system can be used with oxygen, argon, and other reducing gases for versatile applications. Furthermore, by utilizing RIE mode, the ashing rate can be further increased. Evaluations will continue, and future updates will be reported in subsequent publications.